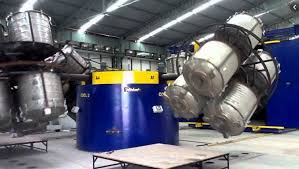
Rotational Molding , or even rotomolding , is actually progressively more named an excellent making opportinity for creating heavy-duty plastic parts. This method, that needs heating up along with folding the mildew to be able to uniformly send out plastic product, offers numerous positive aspects within generating solid ingredients that has to resist challenging conditions. Via industrial system so that you can open-air products, Rotational Molding offers muscle, strength, and layout freedom, which makes it a significant technique for developing heavy-duty parts.
1. Improved Resilience with regard to Tough Surroundings
Heavy-duty plastic material areas frequently want to endure extreme actual worry, heat range fluctuations, plus unpleasant environment conditions. Rotational molding excels throughout making sections that are proof against impression, UV destruction, in addition to corrosion. The task ends up with wide, uniform wall surfaces that help with your device’s toughness as well as longevity. Consequently, rotomolded heavy-duty components—for instance safe-keeping dive bombs, storage units, and also protective housings—will be able to keep its reliability inside businesses similar to agriculture, construction, as well as transportation.
2. Consistent Wall Breadth with regard to Structurel Ethics
One of the important advantages of rotomolding is actually being able to develop pieces having a consistent retaining wall thickness. That persistence can be necessary for heavy-duty applications, when sloping wall membrane depth can produce fragile blotches in which bargain the actual power along with usefulness of the part. Rotomolding makes certain that each percentage of part is based to withstand the stress plus pressure it will experience, rendering it a stable resolution pertaining to making resilient, heavy-duty products that accomplish reliably more than time.
3. Cost-Effective Development to get Big Elements
Producing heavy-duty components generally necessitates important substance level, in addition to regular molding solutions can result in high generation costs. Rotomolding comes with a cost-effective substitute pertaining to creating large sections, since it needs relatively lower tooling expenses in addition to reduces materials waste. The usage of plastic material powder, which is uniformly dispersed and can be recycled, helps make the process more efficient and cost effective, specifically for custom or maybe low-volume development runs.
Summary
This role with rotational molding throughout the creation of heavy-duty plastic-type parts can be pivotal in industrial sectors in which sturdiness, durability, as well as cost-efficiency are generally essential. Using its ability to make constantly robust, adaptable, and cost-effective parts, rotomolding is still your go-to solution to producers searching for high-performance cheap pieces that could tolerate tricky conditions.